Cannondale Super Fatty M Headshok
Disassembly and reassembly, Step by Step
A guide to removing, dissassembling and reassembling a Cannondale Super Fatty M Headshok
by Nigel Pickard
Please note: I (Sheldon Brown) did NOT write this. I have not worked on one of these forks.
If you get in trouble, don't bother asking me for help, you're on your own!
I'm posting it in hopes that it might be useful to some folks, but I can't give you any assurance of how the job will come out if you choose to attempt it...
THE GOOD STUFF
It can be done. I did all work by myself with no help. It can be a one person job. It's not half as bad as people will lead you to believe, and the design of the fork holds no terrible secrets -conceptually it's actually pretty simple! A cautionary note though: I found the job to be pernickety in the sense you had to do some stuff in the right order, and it makes a difference if you do. All I can say is that the order I've listed is the order I found that worked for me, and usually there's a method in the madness for a reason.
Total cost for me to regrease, put a boot on, install new needle bearings and firm ride springkit and purchase any tools I needed: about $70. It took me about 8-10 hours in total to disassemble, reassemble, disassemble and reassemble again (includes thorough degreasing and cleaning). Admittedly, I do have some tools already, but everything else I needed I use in the general maintenance of bikes and is not Cannondale specific (e.g. hammer, Slick Honey grease, Pedros degreaser, etc).
CAVEATS
Caveat number 1:
Basically I had nothing to lose. If I screwed up this fork or couldn't get if back together, it didn't really matter, I'd just go ebaying and get a set of adaptor cups and a used fork (also keep in mind I believe when you strip a Headshok, Cannondale may consider any warrantees null and void). My primary objective was to disassemble the fork and put it back together. If I could do this, I'd then invest in the necessary Cannondale parts and fit them myself. I had nothing to lose but time here.
Caveat number 2.
Since I do not have access to top secret classified Cannondale documents regarding servicing/assembly of Headshoks, I am not privvy to torque specs or the like. This means that I put this fork back together the best way I could (Cannondale diagrams notwithstanding) using at best some guesswork and "common sense" ("common sense" here is very subjective I know. Let me reveal here I'm not a professional bike mechanic, nor am I a qualified mechanic in any area. What I have done is strip various car/motorcycle engines down and put them back together -working mind you!!!! -and my wife believes I have a natural aptitude for mechanics. Then again, she says I'm really good looking too ;^). I consider myself to be confident at mechanics..... confident in knowing when I'm out of my depth). The point here is that I'm just posting what I did -I am by no means suggesting this is the proper or appropriate way to safely reassemble a Headshok. So here you have it, caveat number 2: You mess with your Headshok at your own risk and this posting does not constitute in any way any endorsed ways of properly servicing or assembling or reassembling Headshoks. I am also not responsible for your costs or damages incurred, personal injuries, first born child, blah blah blah. It's all your responsibility and I can't vouch for the accuracy of this post or be responsible for any mistakes contained within.
Caveat number 3:
I did my work on a Super Fatty M. I have no idea about any other Headshok models, they may be totally different as far as I know. The Super Fatty M is an 80 mm travel spring/elastomer model with variable compression via an allen key adjustment after removing the top cap. It came as standard on my 2001 model year Jekyll.
RESOURCES
OK, before I started this, I combed the internet looking for help. I googled, I yahooed, I did everything I could to search for any variation of the words "Cannondale Headshok Headshock assembly disassembly installation removal" etc. Let me tell you: there isn't much out there. And what there is, is hardly encouraging. Certainly Cannondale provides no technical help in the sense of stripping down a Headshok -just rather weak technical diagrams and advice such as "service at an authorized dealer every 40 hours of use". Hmmmm. Anyway, here are some helpful links I found:
http://www.fastglass.net/bike/headshok/repair.html (also has Cannondale technical diagrams in the archive. This was the site that helped me the most -not least because of the clear directions but also great photos. On the downside -and rather worrying for anyone reading it -it does not include reassembly instructions, nor the disassembly of the bearings and races). http://www.bikeparts.com (has some Cannondale Headshok parts as well as proprietary tools such as the castlenut tool ~$35)
http://www.cannondale.com/bikes/tech/headshok.html (Cannondale's own documents for Headshoks) is no longer available but
J. Mical supplied this copy of the complete Cannondale Headshok service manual.
http://forums.mtbr.com/showthread.php?p=1332068t (thread on Headshok disassembly)
Google search on "headshok disassembly"
Some of the common themes I found in the message boards are:
- don't take a Headshok apart
- if you do, don't ever, ever, ever take apart the needle bearings and races.
Ooops, too late. I've always been a bit pigheaded anyway -and like I said, I had nothing to lose.
TOOLS
- old inner tube (700x23 was the best size I found)
- scissors
- small flat bladed screwdriver
- zip ties
- degreaser
- Slick Honey grease (does not degrade elastomer stuff)
- WD-40 (helped degrease parts)
- Threadlok (missing from photo)
- 11mm open ended wrench
- Green Park SPA1 pin spanner (had to buy this from my local bike store $9)
- hammer
- block of wood
- allen keys
- old front axle
- vise and workbench (well lit!)
- home fashioned castlenut tool out of old door hinge (used a hacksaw and file, as well as a hammer and vise to knock this into shape).
- electrical tape
- rags (missing from photo)
- paper towels (missing from photo)
- plastic ziplock bags (missing from photo)
- outer race holding tool (fancy name for an approximately 15cm length of 700x23 inner tube with valve very close to one end, zip tied at both ends)
PARTS
Here are the parts I bought with approximate prices:
- firm ride spring kit $35
- replacement boot $10
- new needle bearings $16*
*worth noting here, for anybody in the greater Boston, Massachusetts area, I looked up the cost of needle bearings online, and found them for $27 at bikeparts.com. After calling three local Cannondale dealers, I found them in stock at Bikeway Source (http://www.bikewaysource.com/), Bedford, Massachusetts. I talked with Eric -a very nice guy -so I'm giving Bikeway a plug here for good service. Thanks Eric!

THE MECHANICKY BIT
Just before I delve into my step by step on how I disassembled and reassembled, I want to add I will call parts by the names designated on the Cannondale technical diagrams. If they are not identified on the diagrams by Cannondale, I'll do my best to describe what I'm referring to. It might be a good idea to have the Cannondale technical diagrams printed out in front of you. I did not find any left handed threads on any of the parts.

SUPER FATTY M -OVERVIEW (YOU NEED TO READ THIS...... NO REALLY!!!!!!)
Let me try to do this as succinctly as possible: conceptually, you can think of the Fatty M as two cylinders, one inside the other. In between the two cylinders are four sets of long rectangular needle roller bearings set equidistantly along the circumference of inner cylinder and lengthwise down the cylinders. These bearings allow the two cylinders to glide effortlessly between each other. Now, instead of these bearings hitting the metals sides of these cylinders directly, there are long metal strips (races) on each side of the needle roller bearings. Hopefully, you're still with me -look at the Cannondale technical diagram to get a better idea here:
Bear with me (oooh terrible pun) -remember I put at the title "YOU NEED TO READ THIS......NO REALLY!!!!!" -well this is the bit you need to know about_: You have four long rectangular bearings. You have 8 races (four on the inner cylinder, four on the outer cylinder. These races are of fine tolerances -and like most things mechanical, you are best putting them back together the WAY THEY WERE PUT TOGETHER INITIALLY. So this means that however you disassemble or assemble the fork, you should try to keep the same races in the same position and orientation. Please, please, remember this. This should be engrained in your brain when you are working on your Headshok. I can't stress this enough (well, actually, that's not true, but it's the bloody easy way to do this, and you don't want the hard way). Of course if you screw this up like me......
STEP BY STEP DISASSEMBLY

- disconnect all hardware from fork (e.g. front disc brake cable, cyclocomputer wire, etc).
- remove front wheel
- either remove brakes, or wrap with plastic ziplock bag to prevent any accidental contamination of brake pads (I wrapped my disc brake with a ziplock bag secured with electrical tape). A little side note here: I can't recommend enough that when you are working on something, if you have the opportunity to protect a part that is likely to be damaged by knocks or contaminants, take the time to protect it or remove it out of harms way. It'll save so much time in the long run and usually provide you with easier access and ultimately give you a much better temperament to work on things. On a nostalgic note, I remember my father showing me how it was so much easier to remove the hood/bonnet of a car to work on the engine if you were going to work on it for a long time. Thanks dad, a lesson learnt and not forgotten.
- Remove top cap using allen key. Put aside safely in a clean box for the parts.
Another side note here: find a clean box to put parts in. I wish I could practice what I'm preaching here, but alas, I can't tell you how many times I've put a part down, and the "Small Part Pixies" come out with their magic dust and thieving grubby little hands -spiriting the part away right from under my own eyes. Putting the parts away safely makes it so much easier -I just really wish I could apply that myself!
- Remove stem from steer tube.
- Place a block of wood on the top of the steerer tube and tap it *gently* with a hammer. The fork should drop out of the headtube.
You should now have the fork in your hands (with brakes removed or protected, right?). The next step is to secure the fork so that you can work on it easily -remember, I said there was only one of me and it can be a one person job:
- Remove the quick release skewer from your front wheel. Put this on your old front axle, and fix your fork to the front axle with the quick release as you would your front wheel. Next, place this axle with fork affixed in your vise (depending on the size of your vise, it might have to go in at an angle -which I actually found was easier anyway) and tighten. The vise should be clamped with enough force to prevent the fork from easily moving. You now have a makeshift way of freeing up your hands to work on the fork!
- Cut the zip ties on the headshok boot, and remove the boot (cutting it off if your are going to replace it) or push the boot down. Again, I recommend wrapping the boot with a piece of cloth and securing it with electrical tape to reduce the chance of you cutting the boot while your are working.
- Using the Park SPA1 pin spanner, unscrew the aluminium cap from the steerer tube. Be careful; you need to hold down the pin spanner to prevent it slipping (which it will do quite easily -and happened to me. I have a big scratch on the top of this aluminium cap -fortunately it is hidden by the top cap cover so it doesn't matter aesthetically. However, for future disassembly reasons, you don't want the two pin holes to become burred over so be careful). The fork should now slide freely up and down.
- You should now see the aluminium cap attaced to a rod. To remove this cap, slide down the foam spacer, and use an 11mm spanner to hold the rod in place. Use the Park SPA1 pin spanner to turn the aluminium cap anti-clockwise. Place the aluminium cap in your box of parts.
- Pushing down on the fork, you should now see the castlenut about a centimetre down in the steerer tube. To remove this castlenut I used a home fashioned tool out of a door hinge, but you could also use a bladed screwdriver. At this point, if the castlenut is on very tight, rather than burr the castlenut, it might be best to purchase the specific Cannondale castlenut remover tool (http://www.bikeparts.com/search_results.asp?IDCA01146). I was fortunate, I found the castlenut came unscrewed with very little effort. 10. You should now be able to grasp the rod, and pull out the compression assembly with the castlenut. Put this safely away in your parts box (note: if you are upgrading the spring/elastomer to an air unit, the bottom cap at the base of the fork steerer tube is simply a compression fit and obviously needs to be removed as you'll have access to your air valve there. You can just use a socket extension and hammer to knock it out of the steerer tube if necessary). 11. Looking down the outer steerer tube, you should be able to see the four outer races (seemingly not secured in anyway but resting up against the thread at the top of the steerer tube) and inside the inner/fork steerer tube, you should be able to see your suspension spring (greensoft, bluemedium, redstiff). You can use your Park pin spanner to hook on the spring to lift the spring and elastomer assembly out. Put away in your parts box. Now, if you look carefully at the top of the inner/fork steerer tube, you should be able to see the tops of four inner races -secured by a race retention clip (looks like a regular washer with four protruding tabs on the outside where the races are secured).
- Remove the race retention clip using two zip ties and a small flat bladed screw driver.
OK. It's at this point I can proudly proclaim this was an original idea of mine. So much of the stuff I've posted is purloined and gathered from other links, but this one is all my own, so I'm "dead proud" of this. You can use the ends of the zip ties to jam down between the tops of the inner races and side of the tab on the race retention clip, forcing the race back and away from the race retention clip tab. If you do this with two adjacent races, you can then use the flat bladed screwdriver to push up the clip and remove it. Using this method, it took me all of five seconds to get the clip out. A word of caution here: I'm guessing that if you break the retention clip, you could be in trouble, so be gentle. This is also another advantage to using the plastic zip ties as it is less likely you'll brea`k that clip using them.
- Move the fork gently up so you have access to the lower Headshok collar. Use the Park SPA1 pin spanner to unscrew this collar. Other instructions have noted this is secured with thread locking compound (mine unscrewed very easily however). Once unscrewed, I moved the collar as far down as it would go, and secured it by wrapping electrical tape around it. Note: DO NOT MOVE THE FORK UP AND DOWN FROM NOW ON UNTIL SPECIFIED!!!! The races are now totally "unsecured" and will fall out if you pull up on the fork. You DO NOT want to do this yet!!!!!
- Remember from the Super Fatty M overview I said: "keep the same races in the same position and orientation" -well, we're now at that bit where we need to secure the races so they all don't fall apart once we take the fork apart. One important thing here to help ensure everything goes back together exactly the same way -make sure you know which way the steerer tube goes on the fork steerer tube -this can be done by looking to see where the single vent hole goes in relation to the fork. The vent hole is a small hole that allows the air to escape from the suspension assembly. I secured my bottom inner races by simply tightly wrapping electrical tape around them. I also tried to use permanent marker to number the races and positions, but found that I could not get the races clean enough even for the permanent marker to take. I read you could use nail varnish to mark the numbers, but it wasn't my day to do my nails or get a perm, and hence did not have access to it. OK, with the lower inner races secured, we now need to secure the top outer races on the outer steerer tube. This is done by basically blowing up part of an inner tube inside the steerer tube, forcing the races to remain in place. It's really, really easy, and better still, works!!!!! Well, sort of.... read on for a cautionary tale: I was really excited at this point. I'd read about using the piece of inner tube to secure the outer races (brilliant I thought, ingeniously simple), and was well versed in how important it was to keep the races in their original positions and orientations. I found an old inner tube I had (700x23) which I decided was to be my sacrifice to the Cannondale Gods, and cut it about 5 cm up from the valve. Next, I cut past the valve about 25 cm down. Feverishly and with great anticipation I zip tied both ends and test inflated it. Perfect! It looked like a dull fat Lancashire black pudding (sorry, reference here for northern English folk) about 25cm long . Feeling well chuffed with myself for being so fortunate to read about such a clever tip, I deflated it -and hurriedly put it into the top of the steerer tube about 10cm down and re-inflated. I was worried about the races moving, so I pumped it up quite well to make extra sure the fit was a snug one. Sounds good eh?
- Once you have secured the outer races, pull apart the fork -as slowly as you can...... the aim here is to make sure the races stay in position. Keep an eye on lower inner races and if you can see them, the top outer ones. Eventually the fork will seperate, and you will see four long rectangle needle bearings in plastic sleeves come down in between the two races. As far as I know, it doesn't matter the orientation or position of the bearings with respect to each other -though I'd still try to put them back the same way they came out as a matter of course. I ended up fitting new ones as one of my bearings had broken so it didn't matter to me. You should now have three sets of parts: (i) a fork with lower inner/fork races taped on, (ii.) four needle bearing sleeves and (iii.) an outer steer tube with an cut off inner tube inflated and sticking out of the top.
OK, back to my little cautionary disaster story: I had those three sets of parts described just as above. I put down the outer steerer tube with inflated inner tube on my workbench to start degreasing and cleaning the bearings and inner races. Suddenly, there was a huge "POP!!!!" and then the sound of tinkling glass. My god, someone is shooting out the basement window! No.....the cut off inflated inner tube had split open, now looking like a forlorn floppy black rubber banana skin, and the outer races were randomly strewn inside the steerer tube. I said "Oh dear" and then added other far less than parsimonious words of the English language.
If you recall from my description, I had about 15cm of inner tube extending out of the steerer tube, and when I had pumped up the inner tube in my ardour to secure the races...... well the top bit had deformed grotesquely because of the air pressure, which of course had no tyre wall (or steerer tube) to help contain it. So here's my lesson learnt: use a lesser length of inner tube (about 10cm), and have as little protruding out of the top as possible -this way, the inner tube should not burst. Also, don't be over zealous with the inflation. So, my dilemma now was I'd royally screwed up the order of the outer races. How could I put them back together again in the right place and orientation? All I can say is that in the end, I tried looking at marks on the races and matching them up to marks in the steerer tube. Honestly, I'm really not too sure I put them back in the exact same place, but what I can say is that my Headshok is smoother now or is as smooth as the day I bought the bike. I suppose the moral of the story is that even if you do lose the positioning of the races, don't give up, it's worth guessing and using a bit of detective work to hopefully reassemble them in the right way. And even if you don't put them back in the original places, it doesn't mean the Headshok won't work.
- Finally, you should now be free to liberally degrease all parts and get them clean. Cannondale recommends you inspect the steerer tube parts for fractures or damage (bit of common sense there I'd say).
Part 3
STEP BY STEP -REASSEMBLY

Assuming the fork is still secured in the vise.....
- If you need to fit a new boot, remove the lower collar, and fit the boot over the fork steerer tube and push it all the way down. Secure the boot and protect it by wrapping a cloth around it (again, I secured the cloth by wrapping electrical tape around it). Check twice to make sure you have the fork boot the right way and replace the collar (once again, secure the collar and double check to make sure you have everything on the correct way!). One open question here: it would seem to me to be extremely awkward and painful to replace a boot without pretty much having to disassemble the entire fork -including the bearings. I tried to find the answer to this question online, but had no luck. It would be crazy if this were the case -but for the life of me I wouldn't like to try to force the boot over the outer steerer tube -which is a very tight squeeze and what you would have to do if you did not totally disassemble the fork. Since I was totally disassembling the fork, I can't say I spent too much time worrying about this -but if my boot splits in the future..... do I have to disassemble my fork again? I wonder.
- Lightly grease the inner and outer races (I used Slick Honey -it will not degrade elastomers). I also lightly greased under the races to help prevent corrosion.
- Using inner tube bands cut to about 1-2cm wide, place these over the lower races on the inner/fork steerer tube to further secure them. Place an inner tube band about 3cm down from the top of the inner/fork steerer tube.
- Taking each of the four bearings, gently guide the needle bearing onto the inner race, and underneath the top inner tube band. Be careful here as the needle bearings are just plastic and delicate, and can be easily broken. Just so you know, the cross section of the needle bearing looks like a long thin rectangle -with the top left and top right corners chopped off. I doubt you can put them in the wrong way, but just in case, the longer flat length goes against the inner race, and the shorter top length goes against the outer race -as I said, I have a feeling you can't fit them any other way, but I thought it was worth mentioning just in case. 5. Each needle bearing should have about 11 needle roller bearings or about half the length of the needle bearing sleeve above the top of the inner/fork steerer tube. Once all four of the needle bearings are in place, lightly grease them (by not greasing them until they are secured, it is easier to work with them). I further secured the needle bearings by using electrical tape wrapped tight around. A tip here: for easy removal -which you'll need to do in a minute -leave the last of the tape sticking out so you can easily get hold of it.
- Here's the tricky bit; putting the outer steerer tube together with the needle bearings and inner/fork steerer tube. Before you do so, quickly check all the races look like they are in position, and you might also need to put some more air in the inflated inner tube holding the outer races in position. Gently place the top steerer tube over the inner/fork steerer tube with the four bearings and gently pull down. Keep an eye on the inflated inner tube to make sure it is not being pushed out of position along with the outer races. You can also get a bit more grip on the outer races by squeezing the inflated inner tube.
- Once you have about 2-3cm of overlap (you'll feel it if there is anything wrong) you can start to remove the electrical tape and cut inner tube bands to allow the outer steerer tube to slip down. Keep pushing down and removing electrical tape and inner tube bands until the needle bearings are enclosed in the inner/fork and outer steerer tubes. Again, be careful and do not be afraid to restart this process as the needle bearing are only in (fragile) plastic sleeves.
My experience with this: remarkably, my first re-assembly I did went like butter and I could not resist letting out a whoop of exhilaration and complete triumph. I had no problems at all, and in the end this process was mere seconds in doing. Interestingly, the next time I did it when I was installing new bearings, my outer races slipped, and I had to start again -and of course, now everything had a load of grease on it too which made it a little more difficult.....I uttered a more fitting "D'oh" per Homer Simpson. Still, even so, it only took minutes in total. I put this down to my liberal and very enthusiastic use of electrical tape to secure bearings and races, as well as a gentle squeeze on that inflated inner tube to help secure those top outer races.
- Really, if you are this far, the hard bit has been done. The rest is just easy and pretty much just the reverse of the disassembly. To secure the race retention clip, push the fork down so the inner/fork steerer tube is within a centimetre or two of the top of the outer steerer. Using the same old zip tie and flat bladed screwdriver trick (see disassembly step by step), secure the tops of the inner races on to the four retention clip tabs. Using zip ties, it really can be done in seconds.
- Replace the newly relubed spring/elastomer assembly into the steerer tube. Slip on the castle nut and tighten using a flat bladed screwdriver (or I used my own hand made tool). I was unsure of using thread lock here, so I didn't. The ease at which the castlenut unscrewed when I initially disassembled it made me think it was not used, and it's under compression anyway and not likely to unscrew itself. Again, not knowing torque settings, I tightened until if felt "right".
- Using the 11mm open ended spanner, hold the rod of the compression assembly at the top, and use the Park SPA1 pin spanner to screw on and secure the aluminium cap. Once again, I did not use thread lock here, and tightened until it felt "right".
Interesting Super Fatty M note here: this connection from the rod to the aluminium cap became loose on my fork when I originally got it. I believe it occurred when I was trying to preload the spring too much, and I think it effectively forced the rod to turn clockwise (as I was looking down on it) thus effectively unscrewing itself from this aluminum cap. Maybe I should have used thread lock on this, I'm not sure. But I'm confident it's tight enough to not have this issue again, coupled with my new knowledge of the mechanical internals.
- Rethread the lower Headshok collar onto the bottom of the outer steerer tube -make sure both threads are clean, and apply some thread lock. Tighten using the Park SPA1 pin spanner. As previously mentioned, I am unsure of the torque setting here. I just tightened until it felt "right". 12. Nearly there! Before we do anything else, we need to check to make sure the needle bearings are in position. This is done by checking the distance between the top lip of the fork to the bottom of the headshok collar. For Super Fatty M, we're looking for 74-79 mm. Mine was a perfect 78 mm. Here is the official Cannondale document that deals with this:
http://www.cannondale.com/Asset/iu_files/112495_Headshok_Fork_(up_to_2001)_Migration_Check_ Procedure.pdf (pdf download) If you have bearing migration.... what can I say.... start again!
- Finally, lube any exposing races, and reattach the boot and secure with zip ties. Make sure the headset races are nice and clean before putting the fork back on the bike. Replace top cap, fit in bike, reinstall stem, reconnect hardware and you're ready to ride.
I hope this post has helped. I wish it had been around before I started on my own Headshok servicing as (and I think you can tell) it was a learning experience for me as I went along. I've ridden the Jekyll since, and the fork feels fine, but of course, it may be I've done something terribly wrong -hopefully not -but would welcome any feedback or comments. One last thing I know I did do "incorrectly": you may pick up from the photos that the vent hole is positioned on the left hand side of the fork (a product of my exploding inner tube in that I lost track of it's relative position) -I believe it should it placed to the back of the fork. Since I tested it and it seemed to work (i.e. the boot isn't ballooning out with air pressure!) I'm guessing it's OK and I can hear the air being forced out..... so I made the decision to leave it as is.
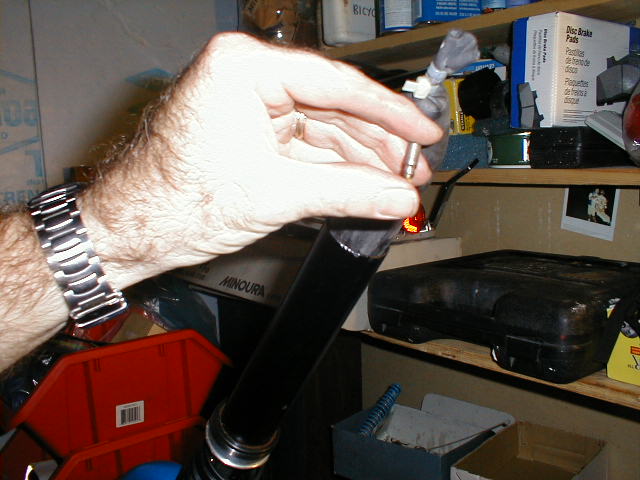
Other pics that might help.... sorry about the order of the pics, I tried to kepp them in order, but it's not easy when you have quite a few and are hurrying up to finish the post......
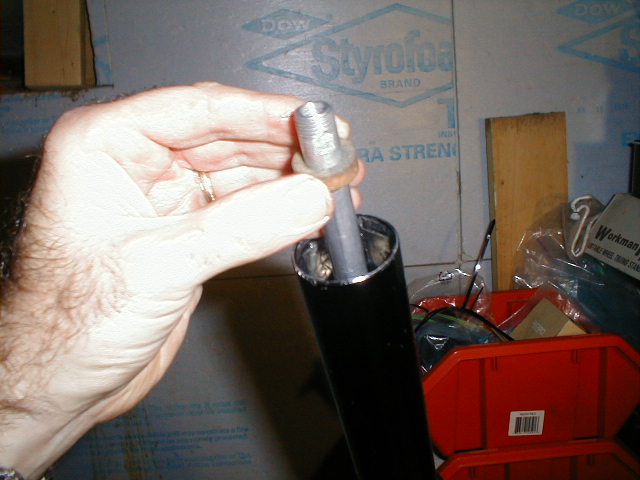
Concerning the bearings, I did put somewhere in that rather overly long missive that 11 bearings or half of the bearing should be above the top of the steerer tube (in the pictures there are, though admittedly at first glance since I wrapped the bottom part of the bearings with electrical tape it may not look like it). I should have also noted I was particularly careful to have all the bearings 11 needles higher than the steerer tube. FYI as well, just one of my bearings -about 1-2cm down at the bottom broke off (maybe even when I was removing it?). I don't think I hit it, just not sure about it. Since the new set of bearings cost so little, I just replaced them all. All in all, I'm really happy as for about $70 I'm back to a much smoother front shock, with a firm spring that is errr... well, more suitable to my middle aged mid riff. I was quite surprized at how many little gotchas I encountered -and how much easier it was if you did some of the little stuff (note here: when putting the outer steerer tube aside with the inflated inner tube, to prevent my kind of experience, also stuff in a rag to keep the races in place in case the inner tube burst! Yep, thought of that later). Lastly, I just love learning new stuff, and that gave me a big satisfaction to know I can adequately service my fork!

Please note: I (Sheldon Brown) did NOT write this. I have not worked on one of these forks.
If you get in trouble, don't bother asking me for help, you're on your own!
I'm posting it in hopes that it might be useful to some folks, but I can't give you any assurance of how the job will come out if you choose to attempt it...
Copyright © 2006 Nigel Pickard
If you would like to make a link or bookmark to this page, the URL is:
http://www.sheldonbrown.com/cannondale-headshok.html
Last Updated: by Harriet Fell